
It was very fragile, even with the base in place to keep its shape. A Spanish windlass would have worked but I had a strap to hand. I used PVA for the mitre joints & a webbing luggage strap to hold it all in compression whilst it set. To determine the height of these, I stacked the acrylic and base together & put them in the assembled box - the remaining height was the height needed. In the meantime, the UPVC came my way and I cut this into strips. I could have painted it or any other coating, I just like oiled wood. Then I painted the base - 1 coat primer undercoat & 2 gloss coats and oiled the oak - about three coats of Danish Oil. I cut the plywood for the base to the same size. I then weighted it down with a heavy thing (sewing machine on a couple of large-format books). I tested cyanoacrylate glue to see how well it worked & was satisfied, so I fairly liberally smeared this onto a sheet or acrylic & quickly put the other on top. I cut two identical pieces of the acrylic sheet. The acrylic sheet was too thin, at 2mm so I planned to laminate two (ore more layers). I could have gone with a bit less than 40mm height, but wasn't about to rip nearly 2 metres of oak strip for that.Īs I had decided to mitre the corners, I had to add the thickness of the strip to my desired surface size & all the hassle that goes with mitring: I wish I hadn't bothered now as they don't look that great & added a lot of time to the build. This set my minimum box thickness.Īfter a bit of indecision as to which wood to use, I plumped for some thin light oak strip which was 5mm x about 40mm.

I experimented to see how close the paper could go to the LEDs without having discernable light points through my art paper (Arches Aquarelle 300gsm/140lb). I had decided that I wanted the box surface to be a tad bigger than A3, which is 297 x 420mm. Would be easier with the proper tool, but very doable with a standard Stanley knife. You have to be bold here - just make lots of scores, the deeper the better. The acrylic was cut with a Stanley knife against a metal ruler - scored then snapped across a workmate edge. Other parts were cut with a standard panel saw - I used a 22 teeth per inch as the plywood was prone to splintering as it was nearly antique. I mitred the corners using a friends bench chopsaw, but in hindsight, I might have been better off just butt-jointing (original plan) as the saw wasn't really accurate enough. Soldering Iron, wire strippers, solder, magnifying light (I'm old & can't see the small soldering bits) Glue: PVA, contact adhesive & cyanoacrylate I scrounged a piece of UPVC trim, which saved me having to paint the inside walls - not a big deal as I had been going to cut some ply for these. Or thicker timber, routed to make rebates for the base & top but I wanted to avoid that level of finesse & mess as I haven't got a dedicated workshop.
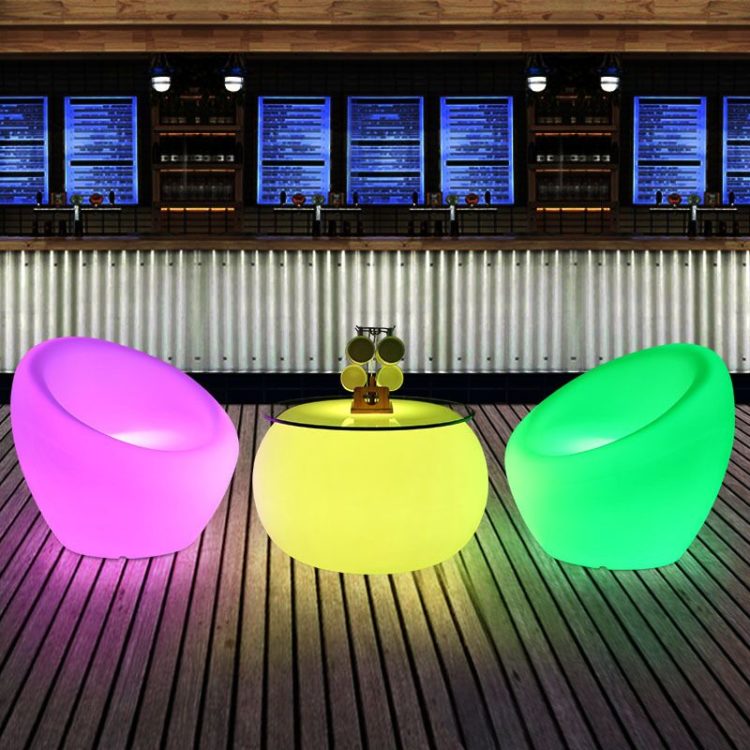
Hardboard (Masonite?) would have done for the base & the sides could have been cut from plywood.

I had sheet plywood in stock - the base came from plywood which had been the back of an old sideboard. I went for cool white, but that is probably a personal thing - it just seemed that they would shine through the cream-coloured paper better?Ī friend was clearing out her garage & I came away with a modest sheet of 2mm acrylic and some misc hardwood strips. I went for 3528 package LEDs as you get more to the metre - therefore a more even spread, than the 5050. Would have been £5 without the PSU, but I wasn't sure if I had the right spec one in my box.
